Optimizing Carbon Brush Life with Condition Monitoring: Sensor Data Acquisition vs. Stand-Alone Sensor Gateways
In industry, ensuring the longevity of critical components like carbon brushes in DC machines is vital – not just for operational efficiency but also for reducing long-term maintenance costs. As Chuck Yung highlights in "Brush Stagger to Optimize Brush Life Through Current Density," the right current density is key to maximizing carbon brush lifespan. Effective condition monitoring systems allow companies to maintain optimal operating conditions for these brushes, translating to significant cost savings and reduced downtime. This article compares two popular solutions—Sensor Data Acquisition (DAQ) systems and stand-alone sensor gateways—illustrating how each approach helps businesses optimize brush life and achieve greater operational benefits, while contributing to improved energy efficiency.
Current Density, Brush Life, and the Cost of Downtime
Carbon brushes are engineered to handle specific current densities, and running them outside this optimal range leads to premature wear. Yung’s research emphasizes that brushes designed for 25-50 amps/square inch can fail in just weeks if operated at lower current densities like 10-15 amps/square inch. Without proper monitoring, businesses risk not only reduced brush life but also costly downtime and increased maintenance.
By ensuring the right conditions for the brushes—via real-time monitoring of current density and load conditions—companies can unlock the benefit of longer-lasting equipment, reducing maintenance costs and unplanned failures. Moreover, this contributes to energy efficiency by preventing overheating and excessive friction that can result from improper current density, which would otherwise increase energy consumption during operation. Monitoring this in real time provides the assurance that brush life is maximized, supporting a healthier bottom line and more energy-efficient operations.
DAQ Systems That Track, Adapt, and Extend Equipment Life
PLC and SCADA systems provide powerful condition monitoring by integrating sensor data acquisition (DAQ) across a facility into a unified platform. These systems track the current density and load conditions of carbon brushes, allowing operators to adjust operations if needed, minimizing brush wear.
However, while DAQ systems provide valuable insight, the complexity and investment required for their setup can be substantial. Integrating multiple sensors and configuring custom logic for brush monitoring can demand significant resources. More importantly, the ongoing costs of maintaining and scaling these systems can limit their appeal to businesses with more focused needs.
This complexity often leads many manufacturers to remain in reactive maintenance mode rather than proactively managing component health. Simplifying the integration process—by easing the barriers to implementation—can help businesses avoid this pitfall, enabling them to move toward more proactive, cost-effective maintenance practices that enhance operations, reduce overall costs, and improve energy efficiency by preventing inefficient energy spikes due to machine malfunctions.
Plug In, Monitor, Optimize: Stand-Alone Gateways for Proactive Maintenance
Stand-alone sensors with gateways offer a simpler, more affordable alternative. These sensors are designed to monitor key conditions such as vibration and temperature, which are aligned with assessing the health of carbon brushes. The sensors communicate with a gateway that has its own software and supports open industrial protocols like Modbus TCP or OPC-UA, providing comprehensive integration into existing PLC or SCADA systems if future expansion of real-time data usage is needed.
The real benefit here lies in the simplicity of deployment. Stand-alone solutions require minimal configuration, reducing the complexity and costs associated with integrating DAQ systems. For example, a stand-alone sensor gateway can track the temperature of the rotating equipment and surrounding components. By continuously monitoring temperature, maintenance operations can identify when brushes are malfunctioning due to issues like improper current density or excessive friction. If temperatures rise beyond safe operating limits, operators can quickly take corrective action to prevent damage, thus maximizing brush life and reducing the energy inefficiency that could arise from overheating. Similarly, the sensor gateways can detect irregularities due to brush misalignment or uneven wear, which are often linked to improper current density, but don’t directly measure the current flowing through the brush. It could, however, indicate that the brush is either too worn or misaligned due to improper density range.
By monitoring these variables in real time, businesses can extend the life of their brushes, maintain equipment efficiency, and avoid costly replacements or downtime. This practice not only enhances operational reliability but also drives energy savings by reducing the likelihood of inefficient operation and equipment failure, which can otherwise lead to higher energy consumption.
Complexity and Cost Comparison
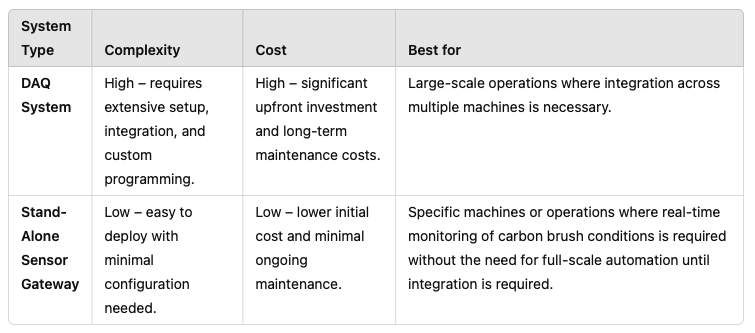
Match the Tool to the Task: Efficiency, Reliability, Cost Control
Both DAQ systems and stand-alone sensor gateways offer unique advantages when it comes to optimizing carbon brush life through effective condition monitoring. For large-scale operations where integration across various machines is needed, DAQ communicating with PLC/SCADA systems provides comprehensive solutions. However, for maintenance operations looking for a more straightforward, cost-effective approach, stand-alone sensor gateways offer the flexibility and simplicity needed to monitor brush health without the complexity and high investment of larger systems.
Choosing the right monitoring solution allows businesses to achieve the ultimate benefit: extending the life of carbon brushes, optimizing performance, reducing downtime, driving long-term cost savings, and enhancing energy efficiency. With the right system in place, maintenance operations can operate more efficiently, with reduced maintenance costs, lower energy consumption, and a stronger, more reliable bottom line.
Pathways7 is a systems consulting firm that contracts with manufacturers and their supply chains to transform their use of information systems.
Critical Machine Parts is our online store that helps manufacturers streamline machine parts replacements through reactive, planned, and predictive maintenance products and services.