From a manufacturer’s point of view, all of IIoT starts with (and typically ends with) "simply communicate if the machine is running or not," because organizational conflicts, technical deficiencies, and cyberphysical security concerns are barriers for larger projects, especially for SMEs. Failed projects have led to disillusion and fear of engaging IIoT initiatives. Projects that have launched quickly taught those that have embarked on the journey that the ability to collect lots of data doesn’t necessarily mean that every data point should be included in strategic metrics. These factors have contributed to the dismemberment of IIoT to the simple goal of machine monitoring – communicate whether the machine is running or not. The problem is that, on its own, on/off status cannot achieve either of maintenance’s or production’s OEE goals.
1) OEE, OOE, and TEEP Rule Operations
"What gets measured gets managed - even when it's pointless to measure and manage it, and even if it harms the purpose of the organisation to do so."
This week, I listened to an IIoT podcast, "Industrial Automation: It Doesn’t Have To… Be Myopic", that reminded me of V. F. Ridgway’s critique of the measurement mantra, "What gets measured gets managed." The conversation was about the importance of machine monitoring through the eyes of an integrator who is an expert at networking data to improve production processes. During the podcast, Brandon Ellis of elliTek describes several application examples of how one piece of data doesn’t provide any insight without corresponding data to provide meaning. Without meaning associated with the data, creating KPIs and strategic actions will at least be futile and at worst cause harm.
My favorite part of Brandon’s explanations are his metaphors in what I’ve heard him call "Tennessee Talk." The one I’m going to focus on in this post is when he offers an explanation about the indicators that matter to production. The example provides insight into how production looks at Key Performance Indicators versus how maintenance might:
"The refrigerator is running." [AVAILABILITY]
"That doesn’t mean there’s food inside;" [PERFORMANCE]
"It doesn’t necessarily mean the food inside is good." [QUALITY]
"It just means the refrigerator is running; so it’s probably cold, but it may be perfectly cold with bad food in it."
The insight for managers is that if maintenance’s machine monitoring data is created to coexist with production’s process data, significant improvement can take place. Without corresponding process data, simple on/off machine monitoring doesn’t have much meaning. Brandon goes on to explain that OEE along with OOE and TEEP are all subjective because manufacturers aren’t all making the same parts. He shares the differences between making tractors versus printed circuit boards versus medical device kits and explains how TEEP includes all the factors for a complete operational picture. Using TEEP for a complete picture of operational effectiveness includes equipment factors like maintaining current equipment or replacing it and people factors like walk-time. With the full picture of production in mind, let’s move on to consider how maintenance KPIs can contribute to operational objectives.
2) KPP for Maintenance KPI relevance
Good indicators aim at continuous improvement not keeping score.
Key Performance Parameters (KPP) are guidance for maintenance KPIs that provide operations the information that’s needed to continually improve processes. "Metrics should be resilient; point to problems, regardless of the hierarchical level; and suggest improvements. Metrics are needed for continuous improvement and shouldn’t be used to intimidate workers or pet egos." Pascual, D. G., & Kumar, U. (2016). Maintenance audits handbook: A performance measurement framework. Boca Raton: CRC Press, Taylor & Francis Group.
Used correctly as part of a company’s TPM strategy, improved maintenance performance can create value for its internal customers and contribute to operational income. KPPs provide guidance about indicators measured for maintenance KPIs.
This book provides both indicators and reference measures, identifying the user or owner of each, setting the basis for external or internal audits. The resulting audit model is mixed. It combines surveys (as the opinions of those involved are important) with numerical indicators obtained from the information systems of the organization.
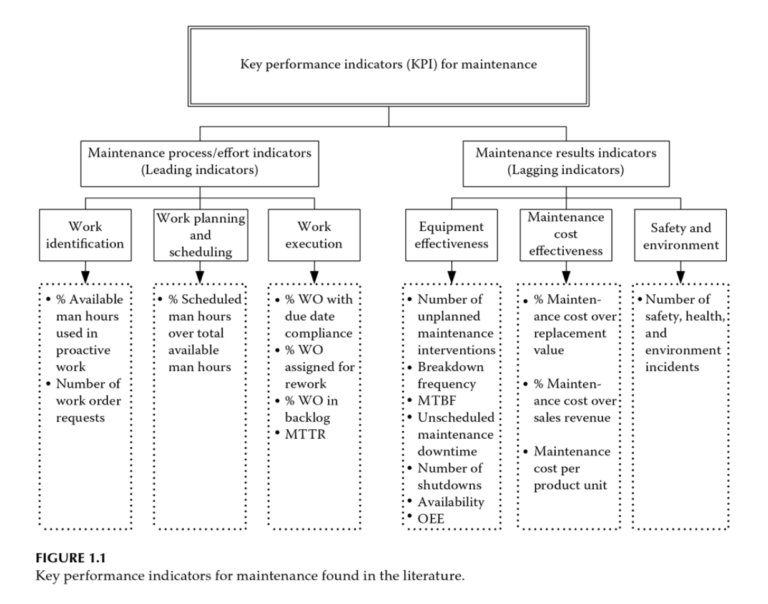
3) Symbiotic Maintenance and Production Data for OEE
Real-time, predictive maintenance (PdM) data that's networked properly integrates with production data for a complete OEE picture.
OEE is defined as Availability x Performance x Quality. This typically is interpreted as Maintenance responsibility x Production responsibility x Production responsibility. The interdependent relationship has some built-in conflict between the two departments. Using the above podcast’s refrigerator example, a conflict exists if maintenance constantly wants to check the refrigerator to ensure every part is working properly and production only wants the machine interrupted when a failing part on the refrigerator (machine) affects the quality of the food it’s meant to ensure (produce).
A simple thought exercise makes the interdepartmental conflict obvious over something as simple as a metaphorical refrigerator:
- Who is in charge of making sure the temperature is correctly measured?
- Who determines if the light going on and off when the door opens affects safety and is a critical maintenance issue?
- Who’s responsible for operators leaving the refrigerator door open consuming inordinate amounts of energy?
I recently read a ReliablePlant article that describes the maintenance/production relationship: "A good analogy is to compare the relationship of production and maintenance with the civilian control of the U.S. military. The military knows how to do its job, but the rules it must work under are determined by civilian authority. Maintenance must realize this and understand that their rules of engagement, such as equipment availability, budget and resources, will be determined by someone else. … Production will always put pressure on maintenance to solve problems, increase machine reliability and reduce costs, and they will want it all to be done now regardless of how unreasonable the demand is."
With a properly networked maintenance information system using well defined KPPs that contribute to organizational KPIs, maintenance departments are able to not only improve their own performance but provide the data required for continuously improving operational success. Predictive maintenance that’s capable of monitoring the vibration, temperature, and current of moving parts reduces the interference of planned maintenance routines. These maintenance routines are at the heart of the conflict between maintenance who’s responsible for preventing machine failures and production who wants equipment available and performing as much as possible. Instead of proposing colloquialisms about maintenance and production singing "Kumbaya", networking solutions from Pathways7 integrate IIoT sensors with CMMS and information systems to empower maintenance departments for a symbiotic relationship with production. Predictive, leading indicators on moving parts reduce machine interruptions and prevent surprise component failures. Along with real-time monitoring, the sensor data is captured and translated to integrate with production’s databases and its software used for tracking OEE and other KPIs. Maintenance KPIs are improved while the production department is able to gain comprehensive insights to achieve their objectives too.
- Secure real-time machine monitoring with predictive indicators.
- Event-based notifications for reduced network traffic and optimized availability.
- Sensor and PLC data reformatted for CMMS and production’s OEE and TEEP software.